Startup Profile
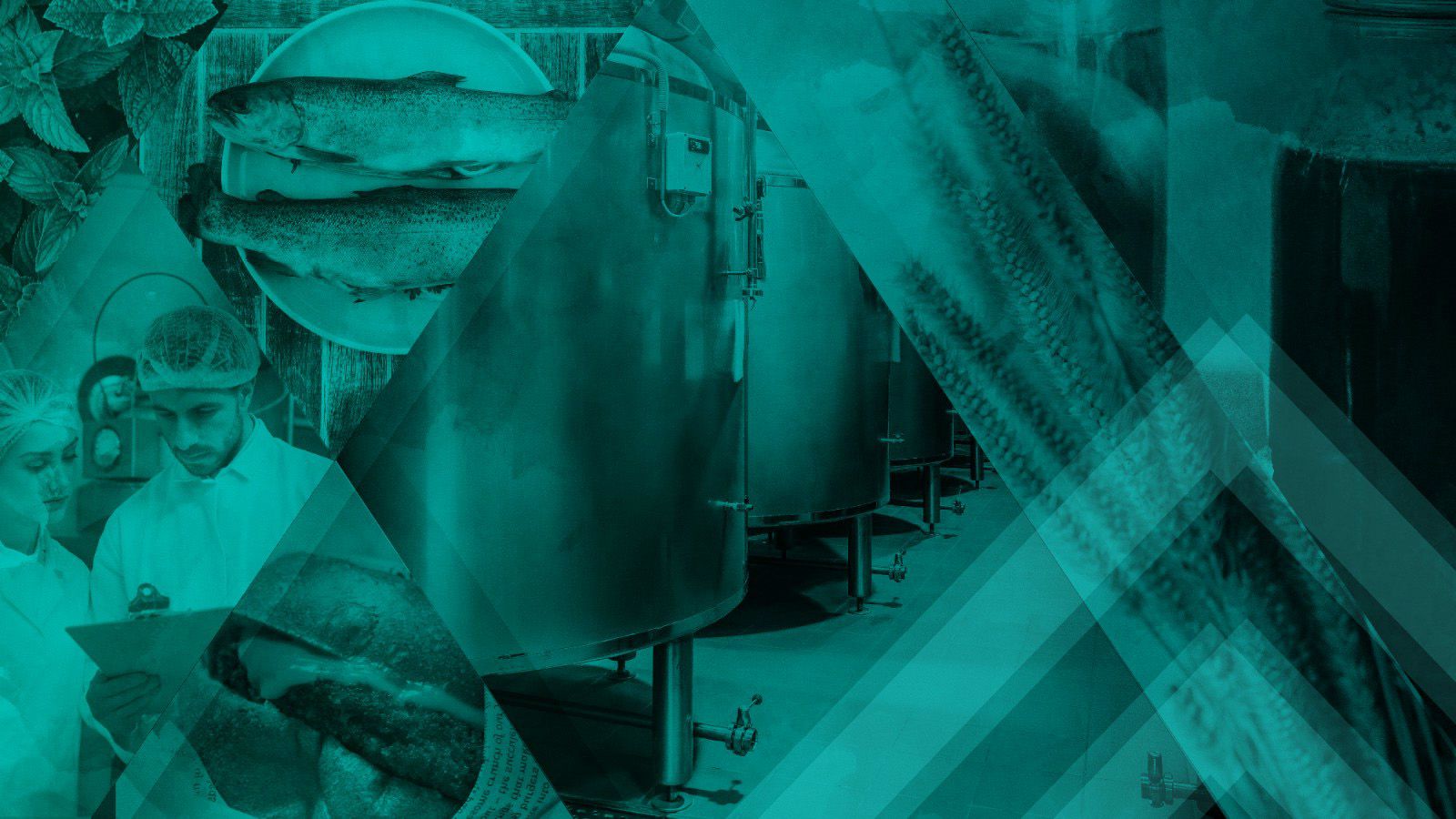
The problem we're solving
Growing food demand due to rising population has led to 1) intensive use of inefficient chemical fertilisers with a high negative environmental impact and 2) increased organic waste generation.
Intensive chemical fertiliser caused increased water streams and air pollution, acidification and salinization of the soil leading to desertification and decreasing yields across different crops, as soil grows infertile.
Organic waste generation faces inefficient, expensive management methods that are energy & water-intensive, generate GHG emissions and have little or no nutrient/waste valorisation: i) Composting loses 50% of carbon as GHG emission and takes up to 6 months to process ii) AD requires high treatment costs, produces hazardous digestate, requires transport and centralised treatment (landfilling/ incineration).
Fertilizer industry is one of the largest GHG emitters, representing 1.2% of global
CO2 emissions, which adds to fertilizer use on the soil (4.1%), waste water (1.3%) or livestock (5.8%)
Our solution
Agristarbio’s BTSys produces organic-mineral fertiliser from the treatment and valorisation of organic waste recycling all its nutrients (100% of minerals nitrogen, potassium, phosphate and organic matter) with zero emissions at a competitive cost.
The fertilizer is produced by a proprietary process in a closed pressured environment recycling all organic matter and nutrients and producing a nutrient customized (NPK) fertilizer with up to 60% of stabilized organic matter. Agristarbio’s chemical reactor promotes a violent reaction that causes cellular lysis, chelation of organic matter with nutrients and, when present, heavy metals.
The reactor fits in a 40 feet container and the unit is 1.500 m2 for a production capacity of 12,000 tons of fertilizer and a processing capacity of 40,000 tons of organic waste.
Our differentiator
Agristarbio is the only one to produce organic mineral fertilizer in small modular facilities, recycling all organic matter and nutrients, installing itself near or inside the waste producer’s facilities.
The fertilizer is unique in terms of its fulvic and humic acids (due to cell lysis during production/ treatment waste) and as well as the controlled release of the nutrients since day of application. With up to 60% of organic matter it protects soil from salinization and acidification, keeping the soil within optimal plant nitrogen uptake.
Biggest achievement
Grants from European Innovation Council (SME phase 1) and EIT European Institute for Innovation & Technology (Booster Call).
Selected for EIT Food Accelerator, BGI, Top 10 Portuguese startup in sustainability by the Portuguese Environmental Fund in 2020.
Registred Fertilizer Ferteen 9-18-9 in 2021 with national economic entitiy (DGAE).
The problem we're solving
Growing food demand due to rising population has led to 1) intensive use of inefficient chemical fertilisers with a high negative environmental impact and 2) increased organic waste generation. Intensive chemical fertiliser caused increased water streams and air pollution, acidification and salinization of the soil leading to desertification and decreasing yields across different crops, as soil grows infertile. Organic waste generation faces inefficient, expensive management methods that are energy & water-intensive, generate GHG emissions and have little or no nutrient/waste valorisation: i) Composting loses 50% of carbon as GHG emission and takes up to 6 months to process ii) AD requires high treatment costs, produces hazardous digestate, requires transport and centralised treatment (landfilling/ incineration). Fertilizer industry is one of the largest GHG emitters, representing 1.2% of global CO2 emissions, which adds to fertilizer use on the soil (4.1%), waste water (1.3%) or livestock (5.8%)
Our solution
Agristarbio’s BTSys produces organic-mineral fertiliser from the treatment and valorisation of organic waste recycling all its nutrients (100% of minerals nitrogen, potassium, phosphate and organic matter) with zero emissions at a competitive cost. The fertilizer is produced by a proprietary process in a closed pressured environment recycling all organic matter and nutrients and producing a nutrient customized (NPK) fertilizer with up to 60% of stabilized organic matter. Agristarbio’s chemical reactor promotes a violent reaction that causes cellular lysis, chelation of organic matter with nutrients and, when present, heavy metals. The reactor fits in a 40 feet container and the unit is 1.500 m2 for a production capacity of 12,000 tons of fertilizer and a processing capacity of 40,000 tons of organic waste.
Our differentiator
Agristarbio is the only one to produce organic mineral fertilizer in small modular facilities, recycling all organic matter and nutrients, installing itself near or inside the waste producer’s facilities. The fertilizer is unique in terms of its fulvic and humic acids (due to cell lysis during production/ treatment waste) and as well as the controlled release of the nutrients since day of application. With up to 60% of organic matter it protects soil from salinization and acidification, keeping the soil within optimal plant nitrogen uptake.